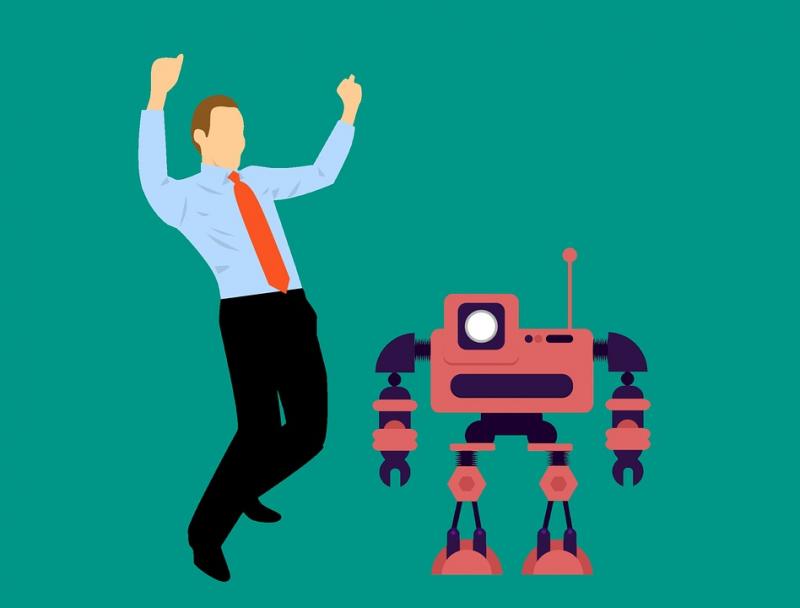
Industrial automation uses control systems from technological resources like computer robots and information technologies to handle different processes and machinery to replace a human being.
In the beginning, the industrial production process is were done by human labor resources depending on the worker's eyes, hands, and brain. Still, today in the modern world, this work can be done by sensors, actuators and computers. Automation in the production process is work on replacing human workers with an independent machine. It can also increase production, and these autonomous machines work under coordination with human supervisor for better results.
Functions of Industrial Automation
Following functions can you perform by industrial automation:
- Increase in the production
- Reducing the cost
- Efficient use of raw material
- Increase business profits
- Reduce energy consumption
- Improve the quality of products
Levels of Industrial Automation
There are some levels of an industrial automation process.
1. Superior Level
It is available at the top of the hierarchy. The superior level consists of an industrial PC available as a desktop PC or some other PCs.
These PCs run on the standard operating system with particular software. It is attached which a supplier that provides industrial process control. The primary function of the software is to provide service visualization and parameterization.
2. Control Level
Control level is a level of hierarchy that controls all the automation related programs. It used programmable logic controller, which provides real-time computing capability. It is usually implemented by using 16-bit 13-bit microcontrollers and carried out the proprietary operating systems to meet the real-time requirements. PLCs are also capable of being interfaced with several devices and can communicate through a various communication protocol.
3. Field Level
The equipment like sensors and actuators are considered in the field level in the hierarchy. These sensors work for detection of temperature, optical, and pressure along with equators like motors and valves etc. The communication between the field level device and programmable logic controllers are usually based on point to point connection.
These components can do work on both wired and wireless communication. Industrial automation process system also requires other methods such as industrial power supply and other one is security and protection.
Read more:
Business Technology Management
Technology Empowerment for Organizations
Pros of Industrial Automation
Following are the pros of industrial automation:
- The quality control checks can be integrated into the production process to produce consistency.
- The work of human labor is replaced by mechanical machinery.
- Some problematic task with a human cannot operate efficiently, such as lifting heavy materials and large loads done by the robotic machinery.
- Production is always fast, and the cost of the product is less.
Cons of Industrial Automation
As with the pros, here are the cons of industrial automation:
- First, due to the increase of automatic machines, the need for human labor is decreased, and as a result, it causes a loss of jobs for humans.
- All the desired work cannot be done by using current technology. Therefore, there is also a need for human workers.
- The cost of an automatic system is very high.
- A skill personal is a basic need for maintenance and service.